So back in March, I just happened upon a local ad – a fibre artist selling her drum carder at a fantastic price. She had had designs to use it to start processing her own fleeces, but having never gotten the fleecey bug, it ended up sitting unused in her studio for about a decade. Oddly enough she had gotten it much the same way – she bought it second hand from a lady who had also not used it (or used it very lightly). The result, me finding my way to it many years later.
I wasn’t in the market for a drum carder, it was one of those things that I thought “well, maybe one day”. I actually wanted to get a hackle before a drum carder because I really love spinning from combed top. But when a deal that good falls into your lap, how can you possibly say no?
The drum carder itself was manufactured in Sifton, Manitoba by a company called Made-Well Mfg Company. They manufactured spinning wheels as well, and started making these drum carders around the 1960’s to early 1970’s. The one I ended up finding looked like it hadn’t been used since it was manufactured – or at least not in any frequent way.
I knew I’d have to change out the carding cloth – the cloth it came with was original (on leather!) and the TPI (tines per inch) on this bad boy was around the 20 mark. I’m not sure what people were carding up in the 1960’s, but something that coarse just was not going to suit my needs. Of course, I gave it a try on a tiny bit of Shetland and Finn – I couldn’t resist after I had gotten home with it I was so excited. Needless to say, I wasn’t thrilled with the neppy mess I got.
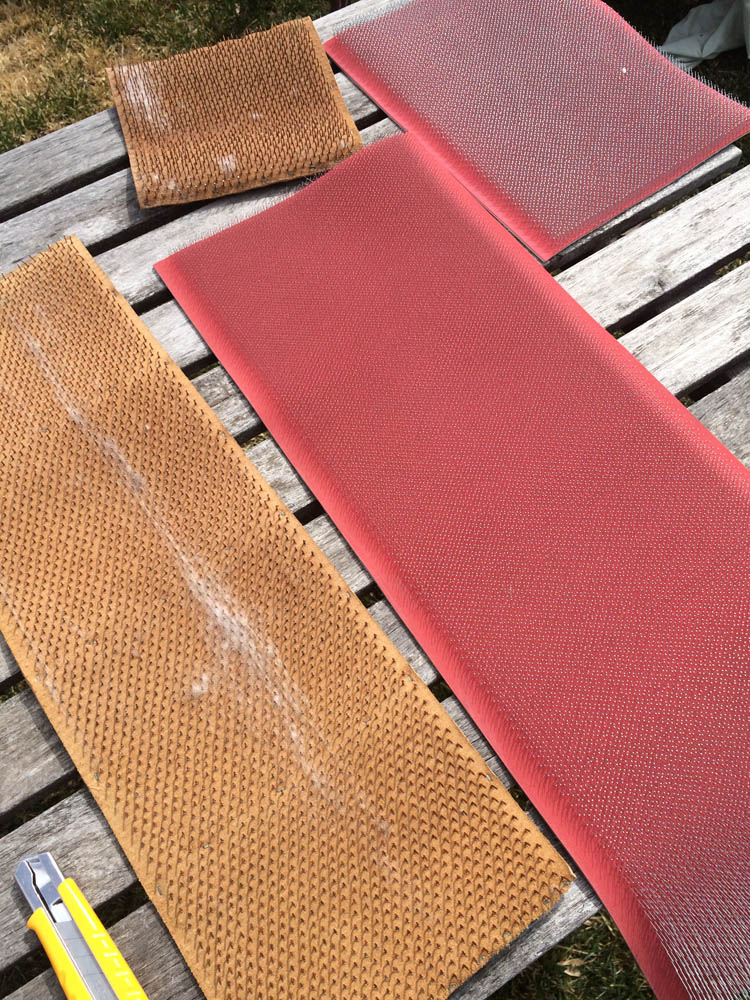
So, fast forward to mid-April and I finally take the plunge and order my carding cloth. Even with exchange the price wasn’t bad, and all in all I’m in for less than half the cost of a new one – including both the cloth and carder. Can’t complain about that, can I?
The first thing I had to do was to take off the old cloth. It looks like it had been attached with hardwood floor staples, so I broke out my slotted screwdriver and pried those suckers off.
Then, I had to cut down my brand new carding cloth to size. This drum carder is not standard due to its age – both the drum and the licker are 7.5″ wide with a 7.25″ carding cloth. So I had to cut the sides way down on the 9.5″ carding cloth I had purchased. With some very careful measuring, and a very (very) sharp box cutter, I cut it down to the size I needed. One thing I learned really quickly – if you’re doing this yourself make sure that you are working with a fresh blade – the backing cloth wears down the knife edge very quickly.
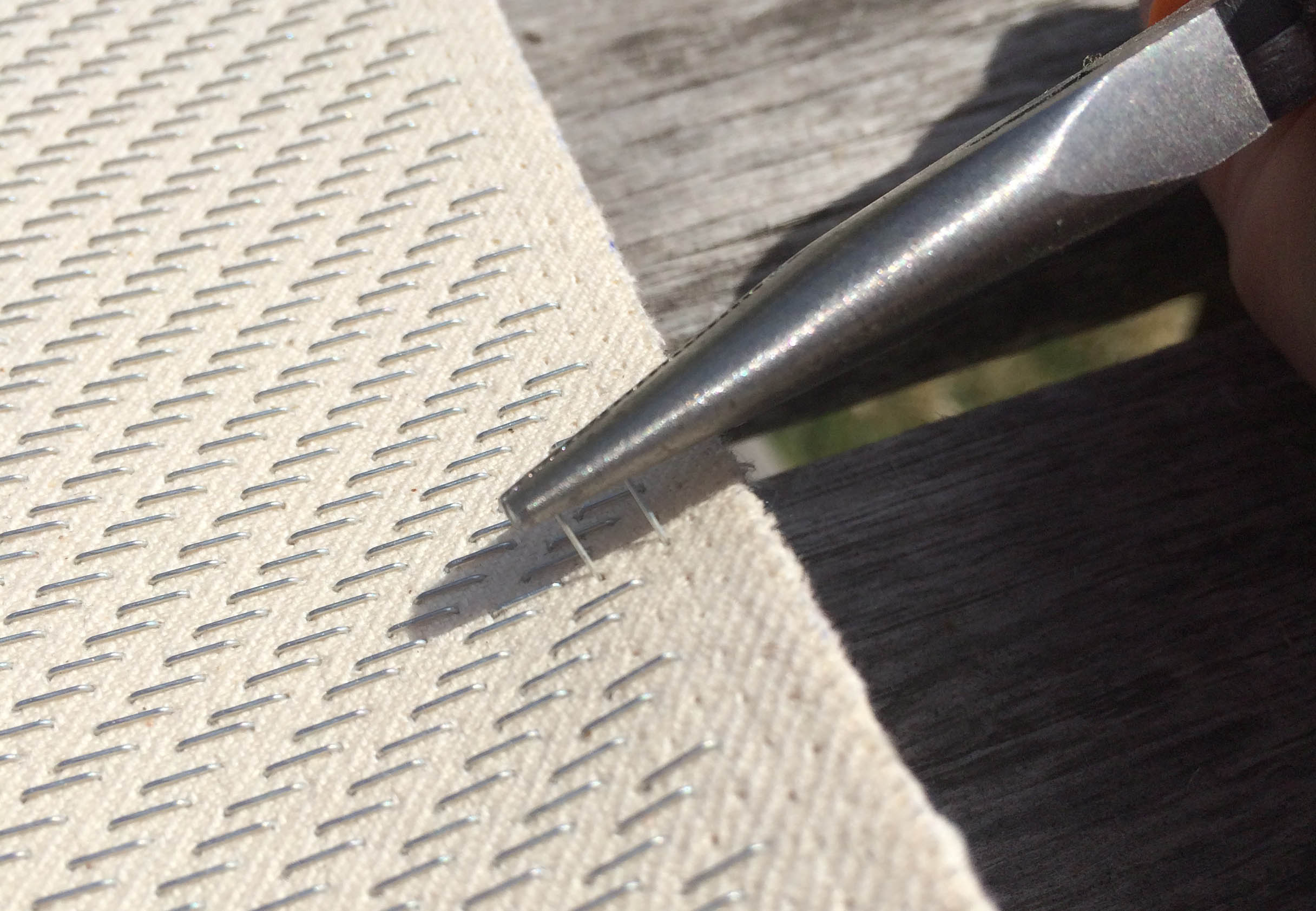
Then came the really tedious task of pulling out tines from 120 tpi cloth to give myself enough edge to staple in. I won’t lie, this was not my favourite part of the process, and it was the part that easily took the most amount of time. Fortunately, I had a beautiful day to sit outside and perform the task, so it wasn’t all bad.
All that was left now was to re-attach the brand new cloth. I used a standard light-weight staple gun for this, and it worked like a charm. But, this is the point where I had some fiddling to do. I had read several blogs, and they all described the same problem – the teeth on the old and new cloth were smashing against the feeder tray, and not only creating a horrible noise, but potentially damaging the tines on the new cloth.
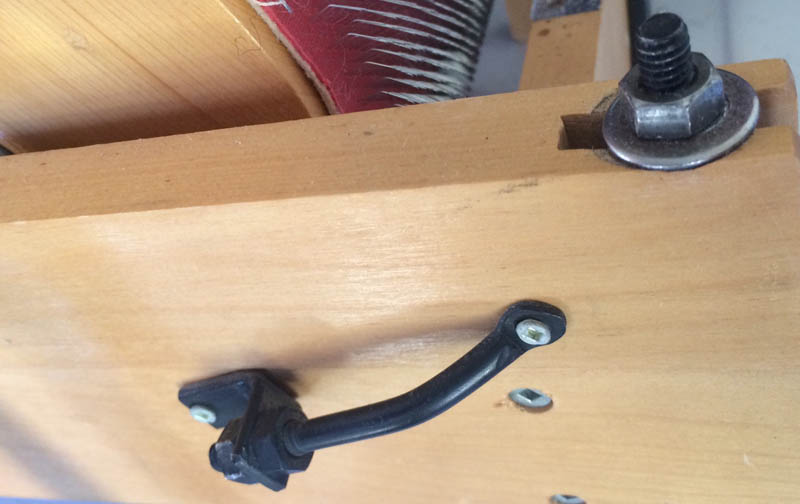
Fortunately, these Made-Well drum carders are slightly adjustable. They have all sorts of nuts and bolts in various locations, so by tightening the bolts that held the drum and lifting the whole apparatus slightly, I was able to move it far enough away to not smash against the feeder, while still allowing it to take in the fibre.
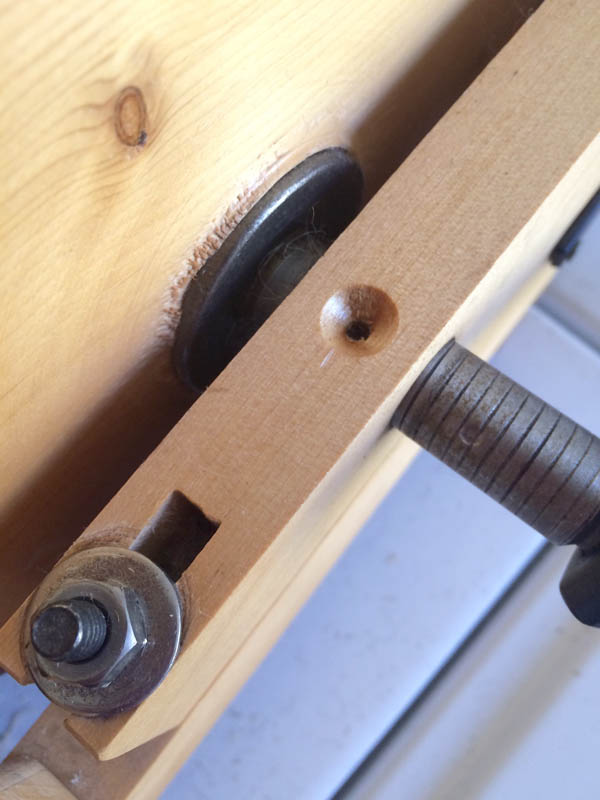
I came off pretty lucky – because this drum carder had such minimal (if any) use since production, there wasn’t a whole lot of refurbishing. While I was disassembling and attaching the carding cloth, I gave everything a bit of a wipe down to clean it, and then once everything was back together I took some of my spinning wheel oil and oiled it up via the ports located on either side of the drum.
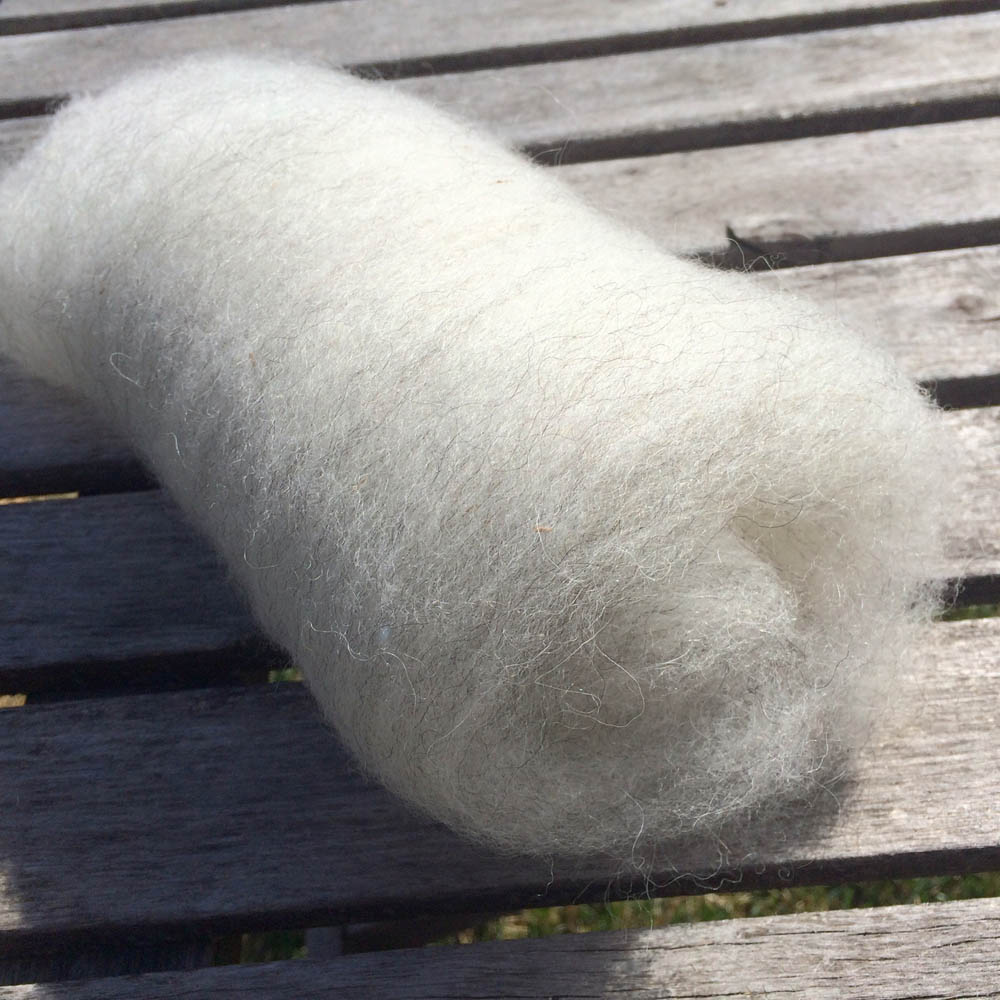
All that was left was to run through some fleece! I had some Shetland that I’d been saving just for this moment, so off I went, putting some through the machine, and I’m over the moon. The batt that came out is worlds different than the nepp-filled fluff that came off when I first got it home. What I have now is beautiful, soft, spinnable wool right off the carder.
What I’m really excited about is the opportunity now I have. I’m not sure carded batts will ever overtake my love of handcombed top, but it does allow me the chance to make more woollen yarns – something I’ve been experimenting in with more frequency in 2018. It also allows for much faster processing of fleeces. Hand combing is lovely, but it’s not the fastest process in the world, and hand combing a whole raw fleece is a huge task (having done it, I can attest to that). But carding up a whole fleece is a much faster process, which in turn opens up more opportunity for spinning up sweater quantities of yarn, which I’m very excited about.
The drum carder also brings me closer to my goal of working at least 90% from locally produced fleeces that I get right from the farmer. It’s something I realized I wanted to do pretty quickly after processing my first fleece, and with the amount of processing I can do with the drum carder, it gets me closer to that goal.